Disc Springs, with all of their variations, are among the most widely used tension generating washers. They are used for spanning alignment holes, distributing bearing loads and for generating and sustaining the tension needed to hold assemblies together.
Belleville washers provide a very high spring force for short movement and have a high energy storage capacity. In a true Belleville washer, the ratio of material thickness to rim width is held to about one in five. Crown height actually should not exceed 40% of material thickness. In application, yield strength is not exceeded and the washer returns to its full crown height when compression force is removed.
Commercial Disc Springs are not held to the specific O.D./crown height/thickness ratios required of the true Belleville Disc Spring washers. Traditionally, the crown height to thickness ratio is considerably greater for commercial Disc Springs. When loaded to flat, their yield point may be exceeded. These washers, however, are often used in applications where they function entirely within their elastic range. In applications where they are loaded beyond their yield point they will act in a consistent manner over a reduced crown height. Such washers have, in effect, become reformed.
By varying thickness and crown height relationships, design engineers meet a wide range of load/deflection requirement with Disc Spring washers. A crown height to thickness ratio ranging from 0.4 to 0.8, for example, produces a fairly constant spring rate (Figure 1).
With a crown height to thickness ratio up to 1.4, the washer will show a positive rate of increase in the load up to 100% deflection (Figure 2).
At a crown height to thickness ratio of 1.4, the Disc Spring shows a constant load over a fairly large deflection, making it useful in applications where extreme wear conditions must be absorbed (Figure 3).
Where the ratio of crown height to thickness exceeds 1.4, yielding will occur and, possibly, oil canning or inverting (Figure 4).
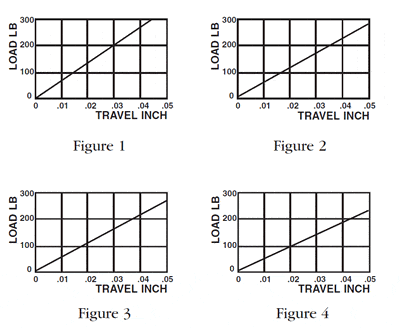
An overall comparison of washer deflection characteristics resulting from load applied to washers with specific height to thickness ratios is shown in Figure 5.
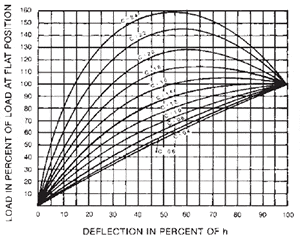
Figure 5
Figure 6
Slotted Disc Springs
Often referred to as a diaphragm spring, the Slotted Disc Spring is used in clutch applications and other applications requiring high travel consistent within acceptable stress limits. The characteristics curve, as shown in figure 6, indicates a relatively constant load over a wide range of deflection.
Stacking
Disc Springs are often stacked to enhance performance characteristics. By stacking them in parallel, load bearing characteristics are enhanced (Figure 7). when stacked in series, greater deflection or travel is achieved (Figure 8).
Combination stacking, in parallel and in series, increases both load bearing and deflection (Figure 9). Disc Springs of varying thicknesses can also be stacked to achieve specific performance objectives (Figure 10).
Comparing Disc Spring Stack To Coil Spring
Figure 11 clearly shows how Disc Springs, stacked in series, support the same load as a coiled spring with a substantial reduction in space required. Disc stacks may be designed for extremely high loads where coil springs are not feasible at all.
Figure 11